CNC Operator-Programmer course (5 days, 50 hours)
conducted fully in English
+ fundamentals of machining technology and technical drawing
Explore this page if you are looking for a course that:
- will thoroughly prepare you from scratch for work as a CNC Operator-Programmer (lathe and milling machine) and develop your machining competences in metals such as steel
- is highly effective while maintaining a good price (20 EUR per 1 hour of training)
- will be held irrespective of the number of registrations (all our course dates published on the website are guaranteed, meaning that they will not be moved or cancelled by us)
- provides the opportunity for practical classes in a machining plant,
- contains the bare minimum of theory required for the job with a high number of practice hours spent with full-sized CNC machines
- is taught by practitioners with many years of experience in the industry, demanding but also able to effectively convey knowledge
- provides certification opportunities through TÜV SÜD, an independent certification body known throughout Europe
- introduces to the operation and programming of the most popular control systems of the industry
- covers the basics of correct interpretation of technical drawings and the use of measuring tools
- provides basic knowledge of machining technology (turning + milling) and ways of selecting tools and parameters for CNC machines
Price: 1099 EUR 999 EUR gross (including 23% VAT)
FIND OUT MORE
-you can read reviews about our courses here
-read more down below, write a chat message to us or call
+48 71 307 36 80
Most popular control systems
You will learn to operate the most common CNC machine tool control systems of the industry.
It is very likely that you will come across one of these while looking for work.
TÜV SÜD certification
A trilingual certificate confirming the expertise acquired during the course. By gaining a certificate from a reputable and well-known institution, you will increase your chances of finding a good job throughout Europe. Among other things, it is characterised by a dedicated holographic strip to protect against falsification attempts.
Work with technical drawings
You will learn how to interpret technical and technological documentation correctly.
This is an essential skill for the correct planning of the machining process and the execution of a workpiece. During the practical classes, you will fabricate actual workpieces – from a saw-cut, semi-finished product to a finished component made according to a fabrication drawing.
Guaranteed training dates and maximum groups of 6 during practice
All our course dates published on the website are guaranteed. This means that it is not possible for them to be transferred or canceled. In addition, we provide students with two modern, industrial machining centers. Classes are conducted in parallel by two instructors, in two groups of a maximum of 6 people.
Confirmed high quality of training
All the training we provide is ISO 9001:2015 quality certified. During the certification process, we met a number of requirements in terms of staff qualifications, the quality and level of training and the teaching equipment of the training rooms for theoretical and practical classes.
Reviews
Training programme
Essential theory and practical exercises (2 days, 20 hours) | The first four days of the course include learning the basics of machining and programming. In order to better prepare trainees for practice and to increase the effectiveness of the training during the course, all topics are discussed through examples and practised using simulators. |
---|---|
Day 1 (8:00 – 18:00) | Technical drawing in machining
Examples of technical documentation encountered in the industry related to machining – discussion Cartesian coordinate system in machining – discussion and exercises with an educational computer software Exercises with simple technical drawings and methods of determining the contour feature points Introduction to machining technology Sinumerik – simulator exercises (ISO programming and overlay: ShopTurn), turning programming based on technical drawings Turning – machining technology Structure and kinematics of a lathe Types of turning tools and characteristics of their geometry (examples) Materials used in the manufacture of cutting tools and their characteristics Geometry of a lathe and its characteristic features (machine coordinate system – MCS) Workpiece coordinate system (WCS) Absolute, incremental and polar dimensioning ISO programme structure (G-code) Programme header Addresses T, D, S, M, F Ways of selecting technological processing parameters Overview of the Sinumerik control system and its functions Sinumerik – simulator exercises (ISO programming and overlay: ShopTurn), turning programming based on technical drawings |
Day 2 (8:00 – 18:00) | Milling – processing technology
Construction and kinematics of a milling machine Types and characteristics of milling tools Milling machine geometry and its characteristic features (machine coordinate system – MCS) Workpiece coordinate system (WCS) Heidenhain iTNC 530 – exercises (ISO programming, based on Klartext and free contours), milling programming based on technical drawings Determining the workpiece zero point (WCS) Linear interpolation (G0, G1) Circular interpolation and finding the radius of curvature (R or CR) Circular interpolation and finding the centre of the circle (I, J, K or U,V,W) Linear and circular interpolation in polar coordinates Working planes (G17, G18, G19) Measuring methods for cutting tools Adding and editing toolboxes (D) Rules for determining units for processing parameters |
Practical training on industrial CNC machines (3 days, 30h) |
Only when equipped with practical knowledge do the course participants begin their training on industrial machining tools as trainees. Classes are taught simultaneously in two groups by two instructors. Each participant has access to a machining tool during training. In order to make the trainees independent, each participant performs individual exercises guided by an instructor. Prior to the start of the course, students receive a basic, safety training by a specialist. The students are divided into two groups with the same programme, as further described. Groups exchange positions at the CNC machines halfway through the day 4 ofthe practical part. |
Day 3 (8:00 – 18:00) |
DMG Mori EcoMill 600V industrial milling centre with Sinumerik 840D control Occupational health and safety training Basic machining tool maintenance Overview of the Sinumerik control system panel and its functions Machine tool operating modes (e.g. JOG, MDI, AUTO) Table of tools and table of zero locations (WCS) Tool measurement – manual and automatic (with tool setting probe) Tool radius compensation and modification of tool correctors (D) Workpiece base measurement – manual and with a touch probe Determining the characteristic features of a workpiece and taking measurements by a touch probe Discussion of various possibilities for safe assembly of the semi-finished product for further machining Assembly of the semi-finished product, inspection of fastening Safe implementation of the machining process Control and analysis of tool arrivals and departures |
Day 4 (8:00 – 18:00) | Working with ready-made machining programs – searching, loading and editing them at a basic level
Checking of the correctness of the machining program using simulation Methods of transferring machining programs between a PC and a CNC machine Machining of elements based on technical documentation and ready-made machining programs Methods of measuring ready elements using various measuring tools Ways to make corrections based on measurement results Practice – Turning Hyundai WIA 230LMA turning machining center with Fanuc 0i control (Manual Guide) Occupational health and safety instruction Overview of the Fanuc 0i control system panel and its functions Machine operating modes (e.g. JOG, MDI, SBK-single block) Tool radius compensation and correctors Tool measurement – manual and using a probe Adding and editing tool correctors (D) Methods of setting the jaws to the required diameter Discussion of various possibilities for safe assembly of the semi-finished product for processing Assembly of the semi-finished product, inspection of fastening Defining and measuring the correct workpiece zero point for the finished machining program Safe implementation of the machining process. Control and analysis of tool arrivals and departures |
Day 5 (8:00 – 18:00) | Working with ready-made machining programs – searching, loading and editing them at a basic level
Checking the correctness of the machining program using simulation Methods of transferring machining programs between a PC and a CNC machine Manufacturing details using a lathe based on technical documentation Methods of measuring manufactured details (various measuring tools) Ways to make corrections based on measurement results The training ends with an exam |
CNC Machines used during practical classes
Hyundai WIA 230LMA
turning centre
———————
Key features:
– rigid construction designed for heavy industrial use
– powered tools
– high-pressure coolant pump (14.5 bar)
– automatic tool measurement sensor
– control systems: Fanuc 0i ManualGuide
DMG Mori EcoMill 600V
milling machining centre
———————
Key features:
– industrial milling machine
– absolute measuring system
– fast, two-arm tool changer
– Reinishaw measuring probe
– Reinishaw tool measurement sensor
– control systems: Sinumerik 840D
Frequently Asked Questions
I don’t yet know which controls I’ll be dealing with in my new job – does it make sense to take the ‘CNC Operator-Programmer’ course at this point?
The training provides the knowledge and skills to not only efficiently operate Sinumerik, Fanuc and Heidenhain controls. Participants learn the programming language for CNC machine tools (G-code) and various procedures for handling numerically controlled lathes and milling machines. Consequently, once the course has been successfully completed, becoming familiar with completely new types of control is not a major problem, as the main principles of their operation are very similar.
Is the certificate I receive after completing the course honoured abroad? What languages is it available in?
Our certificates are recognised abroad. Upon completion of the training, the participant receives 4 separate certificates in Polish, English, German and Dutch. However, it is worthwhile taking advantage of the opportunity to obtain a TÜV SÜD certificate, which further confirms the competences acquired during the course and is issued by an institution with a long tradition of certification.
Why should I choose your course?
During our courses the trainee acquires skills that are not easily available among other CNC training courses in Poland – most importantly, apart from just learning programming, we cover the essential elements of machining technology and teach how to work with industrial machines placing our greatest emphasis on the practical side. Many training companies in Poland run shorter courses with practical classes using small machining tools controlled by ordinary computer software not really used in the industry. Completing such courses allows participants to programme in G-codes at a basic level, but when left alone at the machine and asked to perform specific tasks, e.g. at a job interview – they will throw up their hands helplessly. We try to keep our students out of such situations.
Will the topics covered during the course and the knowledge I will gain make me handle looking for/getting a new job as a CNC Operator-Programmer?
As an answer to this question, it is worth noting that the programme delivered during the course starts with the basics, but does not end there. As a result, the participants acquire skills that will prove essential during a job interview and subsequent work as a CNC operator/programmer.
I found an interesting job advertisement, but the employer already requires 2 years of experience as a CNC milling machine operator. Do I stand a chance of getting this job after taking the course?
The issue of experience required by the employer takes different forms. Due to the precision of the workpieces and/or a high level of complexity of the projects, in is not uncommon that a minimum experience is indisputably required of new CNC operators/programmers. Very often, however, employers take an individual approach to a candidate and then it is a test of their practical skills at a machine that counts If a trainee has not worked with an industrial machining tool – and this is what the employer requires – he or she will fail during an interview even for the less demanding positions. However, if he or she demonstrates knowledge of the controls and quickly grasps new information, the employer may overlook the lack of required experience and hire such a candidate anyway.
How does your course programme relate to current labour market needs? We are talking about the position of a CNC Operator-Programmer.
The course is based on the study of the most common control systems in Poland and Europe. As a result, a vast majority of national and international vacancies for CNC operators/programmers refer to these controllers. Our training programme has been prepared to enable the participant to meet the requirements of the future employer.
Do you have to meet certain requirements to enrol on an operator-programmer course?
Apart from basic computer skills, we have no entry requirements – the course is taught from scratch.
Sign up for a course
Hours per day: | 10h |
Hours total: | 50h |
Theory: | 10h |
Practical training with CNC simulators | 10h |
Practical training with full-size industrial CNC machines | 30h |
Days total: | 5 |
Certificate templates (click to zoom)
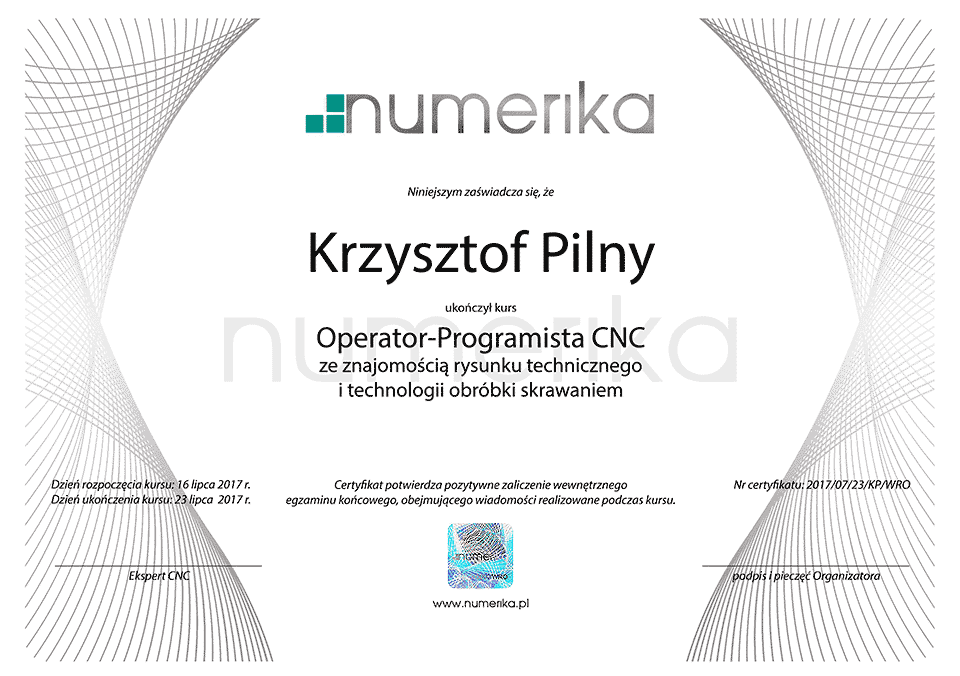
Album | certyfikaty_numerika |
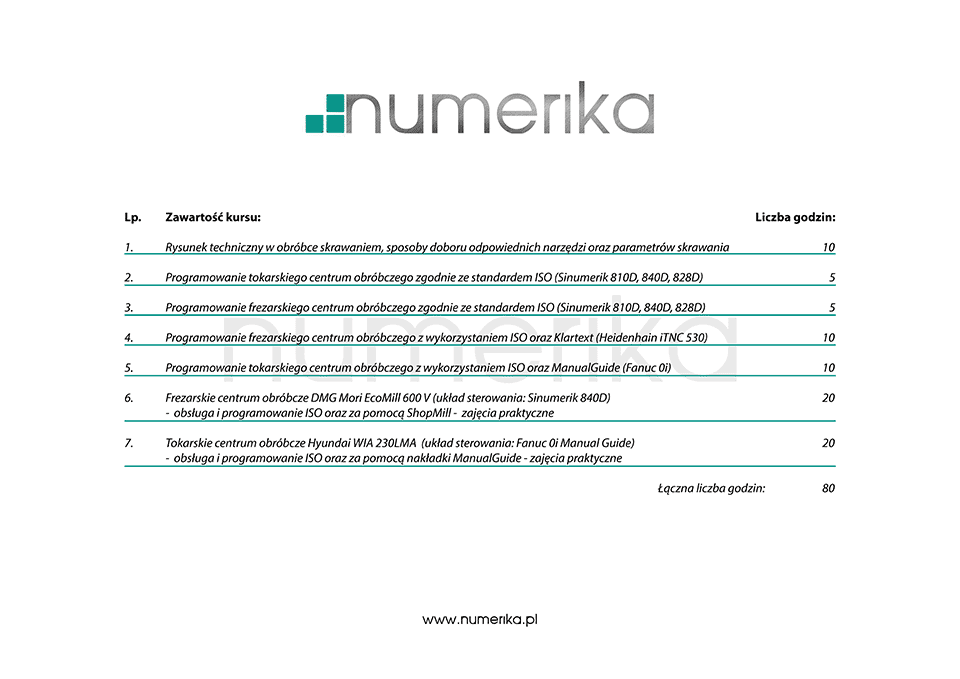
Album | certyfikaty_numerika |